Motion Design has a long history of developing machine products and software that helps streamline laboratory workflows. This area is one of our specialisations and our solutions have been in use in many countries worldwide.
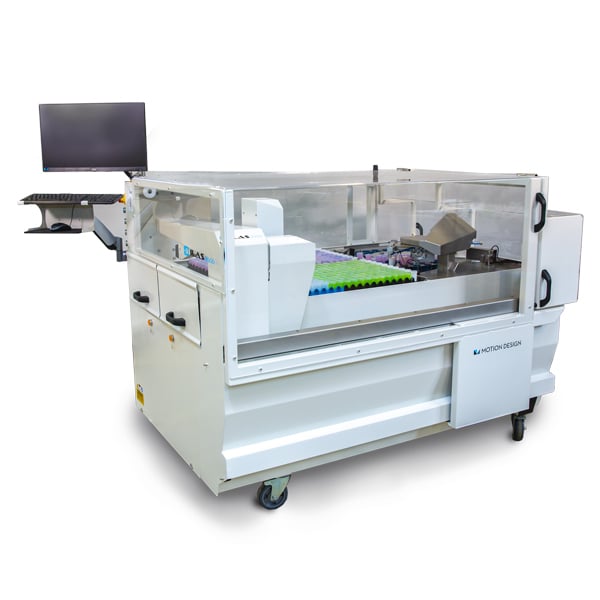
ILAS Waterbath Robot
The ILAS3000 Waterbath Robot is a sample handling automation system for pairing with a “combi” milk analyser.
The ILAS3000 delivers a repeatable and reliable sample warming, mixing and presentation process, improving the quality of test results, while also reducing the labour involved.
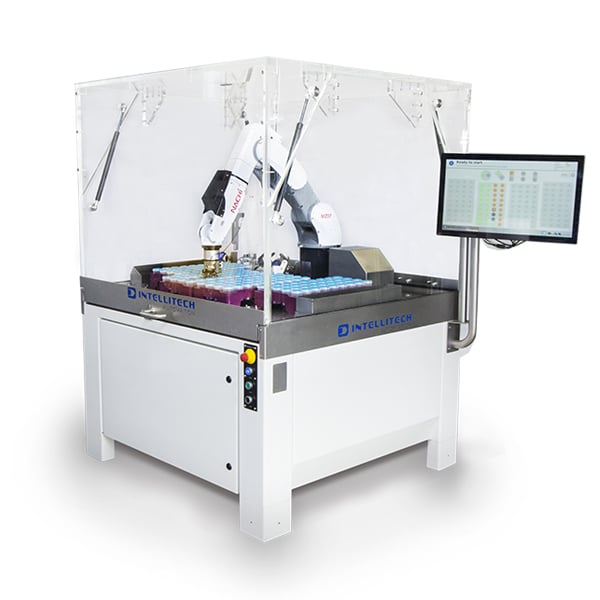
ILAS4000 Bacto Robot
The ILAS4000 Bacto Robot is a sample handling automation system for pairing with a bacteria enumerating milk analyser.
The ILAS4000 delivers a repeatable and reliable sample mixing and presentation process contained within a chilled environment, thus improving the quality of test results, and reducing the labour requirement.
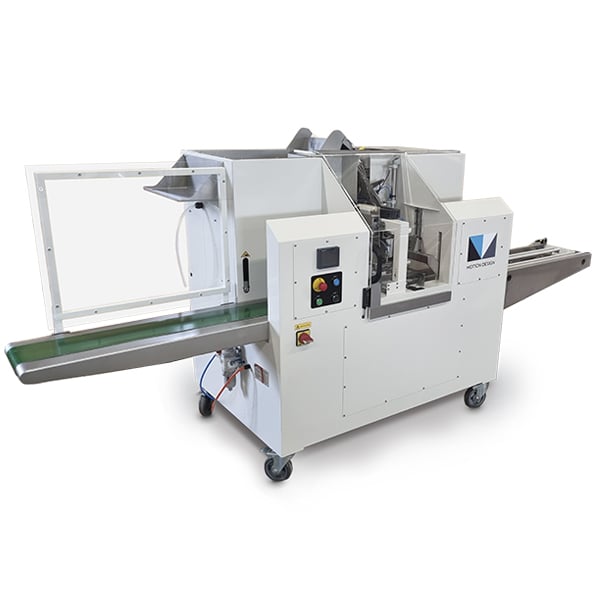
Vial Capping Robot
The Vial Capping Robot automates dispensing liquid bronopol into trays of clean vials, before applying vial caps so that sample vials are ready to go out to farm for sample collection.
Automating this process takes the physical strain away from a highly repetitive task that most Dairy Herd Improvement organisations will be faced with.
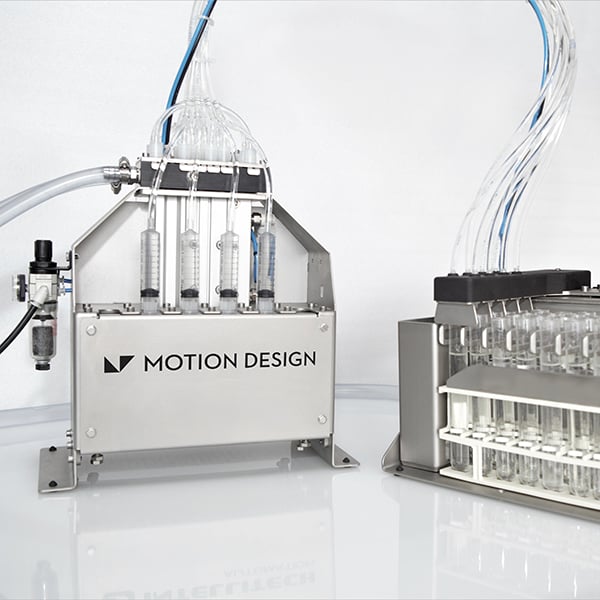
Liquid dispenser
This compact laboratory automation solution is simple yet effective, allowing laboratory technicians to dispense a fixed volume of diluent into multiple vials or test tubes simultaneously, quickly and accurately.
Actuation is entirely pneumatic, and dispensing wands can be hand-held or optionally guided on a linear rail.
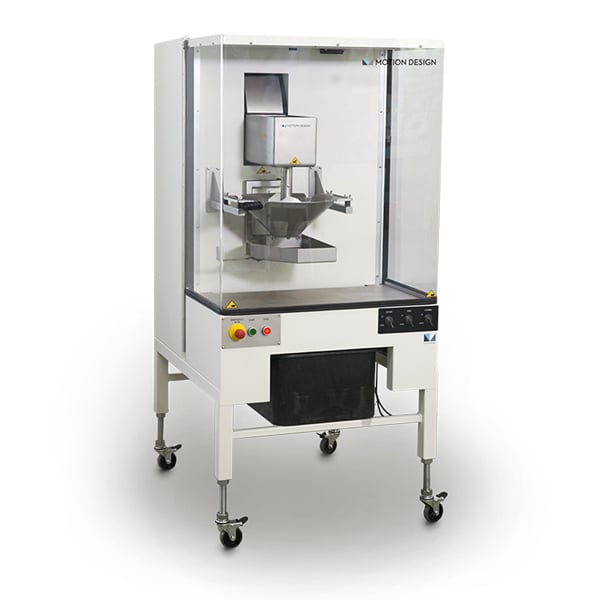
Soil Cone Grinder
Simplify and speed up the tough job of grinding soil samples for Laboratory testing using robotics, with our custom machine the Soil Cone Grinder.
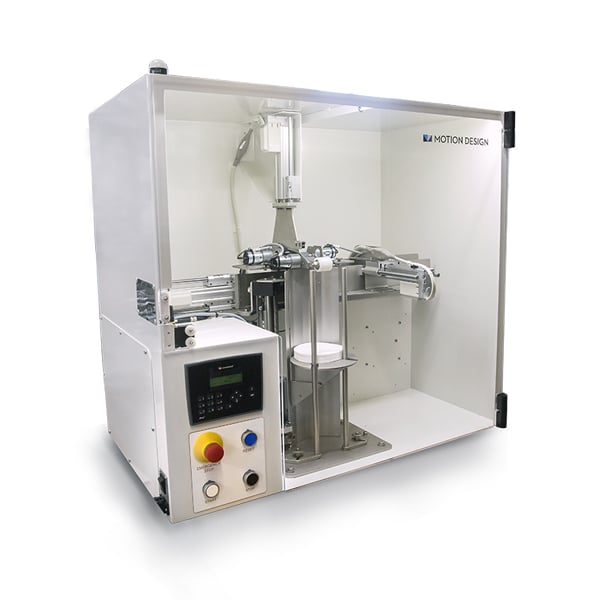
Paper folder
A custom machine that rapidly produces folded filter paper in a reliable, clean, and fully automated manner.
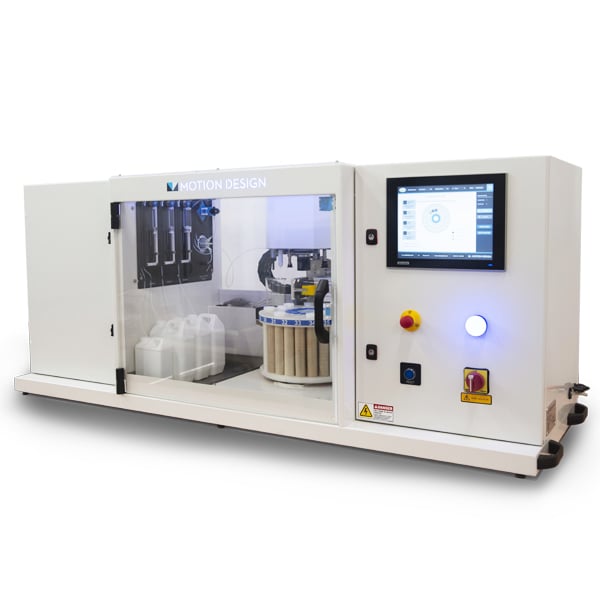
Micro Dispenser
Free up lab technicians and minimise handling of dangerous chemicals with our Micro Dispenser machine. It is designed for use with MARS Microwave Digestion System turntables and vessels and it dispenses via 4 configurable pumps down to +/- 5µl for 500µl dispense.
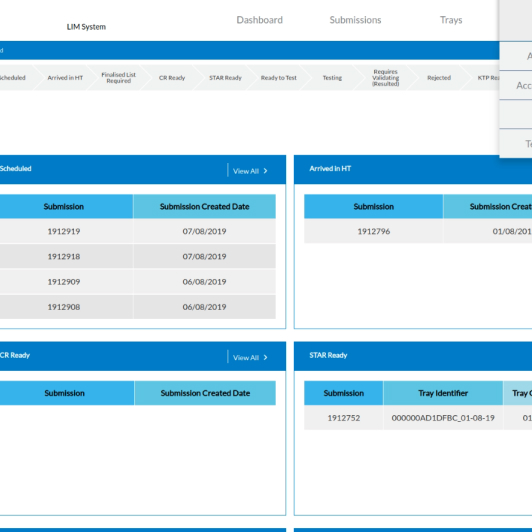
Laboratory Information Management System (LIMS)
With LIMS, labs can streamline processes, achieve faster turnaround times, automate workflows, and improve overall efficiency.
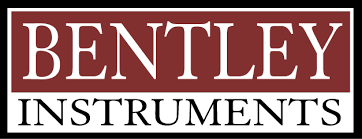
Bentley Instruments
We are proud to be working with Bentley Instruments Inc. to bring their innovative range of milk analysis instruments to New Zealand.
For further information, please contact sales@motiondesign.nz or refer to bentleyinstruments.com
Distributors
Europe
Bentley Instruments SARL
Dans les locaux du laboratoire OXYGEN
840 rue Curie- ZA de BRUNEHAUT
62 161 Maroeuil, France
North America
Bentley Instruments, Inc.
4004 Peavey Rd Chaska
Minnesota 55318 USA
China
Zhong Lao Technologies Ltd
Rm 1209, W3 Oriental Plaza
1 E. Changan Ave, Dongcheng District
Beijing, China
Korea
Samhyuntech
Digital Empire-II, 103Dong-701
88 Sinwon-ro, Yeongtong-gu, Suwon-si,
Gyeonggi-do
Korea.
Zip code: 16681
New Zealand
Head Office
21 Wookey Lane,
Kumeu
Auckland
New Zealand.
Zip code: 0810
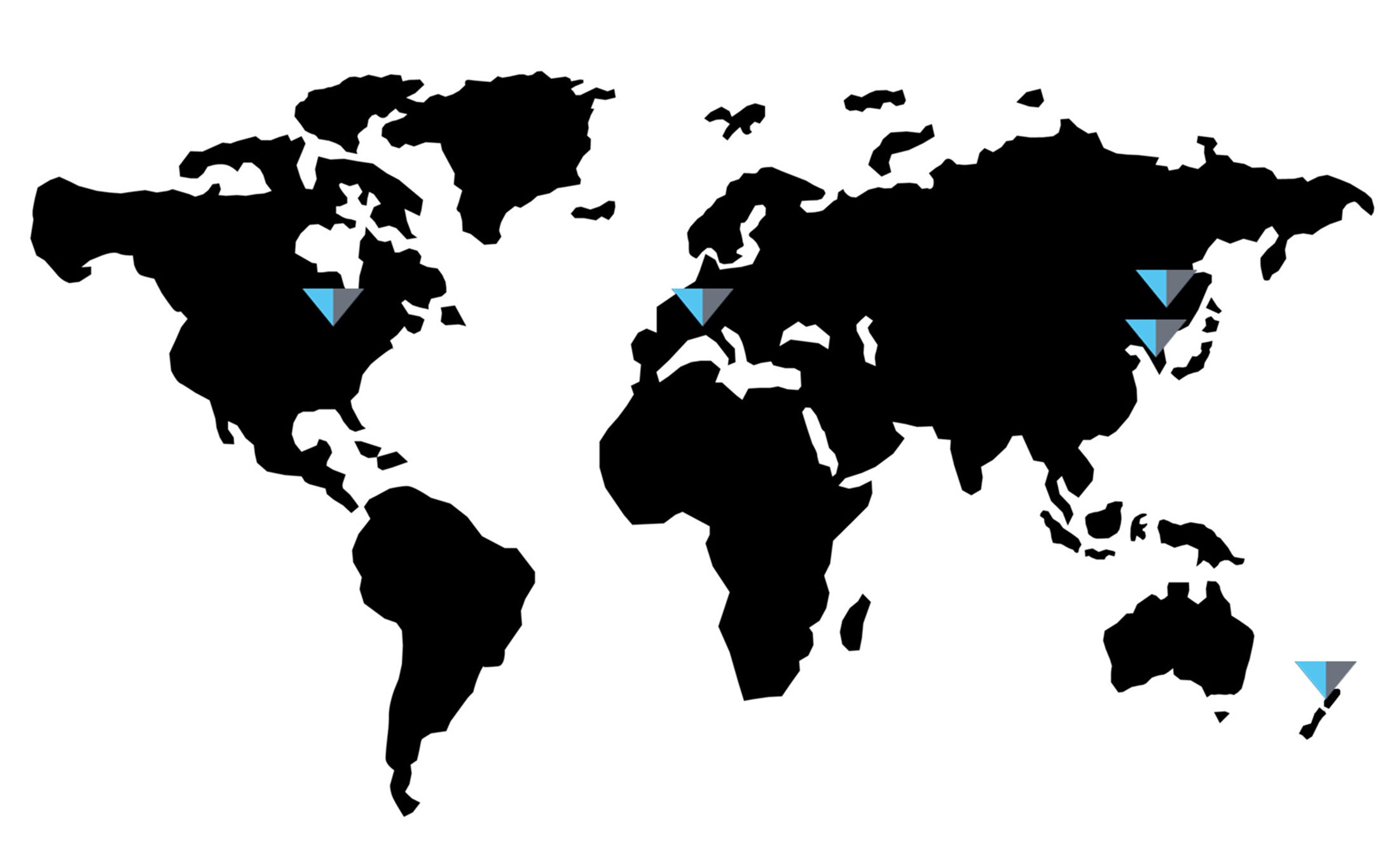